Firmware / Embedded Engineering
In the vast majority of cases, modern products rely on microprocessors and microcontrollers to function as intended. These components manage complex operations that would be impossible to achieve without them. Thanks to the advent of microcontrollers, even relatively small products can now perform sophisticated tasks that were once unthinkable.
At the heart of these systems lies the most critical element: the software—or more precisely, the firmware. This is the set of instructions that dictates how the system behaves, often executing thousands of commands per second in response to various inputs.
Firmware development is a vital and highly specialized area within the broader product development process. Embedded engineers are responsible for translating functional requirements into precise software instruction sets that guide the system's behavior.
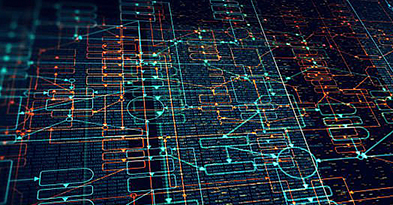
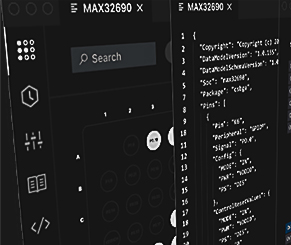
The Embedded Systems Software Development Lifecycle (SDLC)—also referred to as the Embedded Software Development Process—is a structured framework comprising a series of steps and activities used to design, develop, test, deploy and maintain software embedded within a hardware system.
This lifecycle represents a holistic and disciplined approach to managing embedded product development from initial concept through to full-scale production. It integrates both engineering principles and project management best practices to ensure reliability, performance and maintainability.
The SDLC engineering roadmap equips our Developers and System Designers with the tools, methodologies, and resources needed to efficiently create, upgrade and support high-quality embedded solutions tailored to client requirements.
The - Embedded - Firmware Development Process includes a large number of parameters that are not only limited to the intended functionality itself, but also the external parameters in which the system must operate. This means that the system, which must generate conclusion and action, must be all-encompassing. The following explanation describes the process within which a system is developed.
█ Define System Specifications
The system specification defines the hardware and software requirements of the product. This step outlines system features, functionality, performance requirements and other specifications required for developing an effective design of the system.
█ Design Hardware Platform
The hardware platform provides hardware components for developing embedded systems such as microcontrollers, memory, interfaces, and other components. It also provides platform designs such as Schematics, PCB layouts and Bill-of-Materials so we can design a custom-made system based on its specific needs.
█ Develop Software Platform
The included software system is based on operating systems (such as Linux) and middleware, used to develop embedded system applications: i.e. firmware or software applications by using for instance CodeFusion Studio™. During the development we can use commercially available frameworks such as .NET, Android or iOS to develop applications specifically tailored for the intended embedded devices.
█ Design Product
The last step in the Embedded System Development Process involves designing the product's hardware, using a well-defined hardware development document where all aesthetic & mechanical / functional specifications are defined: the Functional Specifications Document (FSD), the Chip Design Documents (CDD), Environmental Specification Document (ESD), Bill-of-Materials (BOM) and so on.
A detailed Technical Design Requirement Specification (TDRS) document should be created as part of the product development process. This document serves as a blueprint for the entire product lifecycle and ensures alignment between engineering, manufacturing and business goals.
The specification should include, but not be limited to, the following key elements:
● Purpose of the Product.
● System Block Diagram.
● Main Features and Functions.
● Environmental Conditions.
● Regulatory and Compliance Requirements.
● Mechanical and Industrial Design Constraints.
● Manufacturing and Testing Requirements.
● Interfaces and Connectivity.
● Power Supply Requirements.
● Firmware and Software Requirements.
A well-structured specification document ensures clarity, reduces miscommunication across teams, and sets a solid foundation for development, validation and manufacturing.
Once the Technical Design Requirement Specification (TDRS) is complete, our software development engineers move on to the detailed design phase. At this stage, each block in the system is analyzed to select appropriate components and finalize the application circuits.
Our software developers and engineers make key decisions such as determining the type of power supply to use—whether it should be a linear regulator, a DC-DC switching converter, or another solution. Based on these decisions, the specific power management ICs (PMICs) are selected and their application circuits are carefully designed & validated. This process is repeated for every functional block in the system to ensure optimal performance, reliability and efficiency.
Here is a systematic breakdown of this process:
█ 1. Requirements & System Architecture
● The Embedded Engineers collaborate with System Architects and Hardware Engineers to define software requirements based on the product’s intended functionality.
● They contribute to shaping the system architecture by advising on microcontroller/microprocessor selection, memory requirements, interface compatibility, and real-time constraints.
█ 2. Hardware Design Phase
● The Embedded Engineers work closely with the Hardware Design Team.
● They review schematics, assist in component selection (e.g., MCUs, sensors, communication modules), and ensure that the hardware supports the intended software features.
● Initial board bring-up code and bootloader frameworks are also developed during this phase.
█ 3. Software Design & Development
● At this stage in the process the Embedded Engineers operate fully on the software development.
● This includes writing low-level drivers, middleware, application logic, communication stacks, integrating real-time operating systems (RTOS), and implementing power management features.
● Emdedded Engineers involvement in iterative development and testing on evaluation boards.
█ 4. Integration & Testing
● The Embedded Engineers test software on actual hardware (prototypes).
● The engineers perform unit testing, integration testing and hardware-in-the-loop (HIL) testing.
● They identify and resolve issues related to hardware-software interactions through in-depth debugging and analysis.
█ 5. Validation, Certification & Production Support
● The Embedded Engineers help with the System Engineers to validate software against the original TDRS, ensure compliance with standards and prepare production-ready firmware.
● Post-production, the Embedded Engineers support the System Design Engineers with firmware updates, bug fixes and feature enhancements (e.g., OTA updates).
Engineers often observe that a product excelling in controlled laboratory environments can encounter unexpected issues upon deployment in real-world scenarios. This occurs because actual operational environments typically present unpredictable variables, vastly different from the controlled conditions of a lab. Therefore, engineers must thoroughly anticipate and simulate these diverse environmental and operational contexts during testing to effectively validate product performance prior to deployment.
One frequently encountered challenge involves signal integrity in high-speed digital interfaces under real-world electromagnetic conditions. In the lab, signal paths are typically optimized with minimal noise and ideal routing, but once deployed, products may suffer from EMI, ground loops or impedance mismatches. For example, differential pairs on a PCB might not maintain controlled impedance due to board layout constraints in production, leading to data errors or communication failures. To address these issues, engineers often implement robust signal conditioning techniques, such as impedance matching, proper termination and the use of common-mode chokes or ferrite beads to filter noise. Simulation and controlled impedance testing help, but field validation remains essential for capturing unforeseen interactions in complex environments.
Wireless connectivity presents another significant challenge. Products relying on LTE+/5G technologies may experience varying signal strengths and inconsistent connectivity depending on local network coverage. Accurately reproducing these complex conditions within lab environments is challenging, necessitating extensive field testing to assess true connectivity performance accurately.
Additionally, environmental influences such as temperature extremes, humidity fluctuations, mechanical vibrations, and pressure variations considerably impact product performance. Comprehensive testing under these diverse conditions is vital to verify product reliability, durability, and functionality in authentic operational environments. Ultimately, extensive field validation remains indispensable.
Once field trials have been conducted over several weeks or months, all insights and feedback gathered must be carefully incorporated into the product design. If any issues are identified during these trials, it's essential not only to address them in the design but also to update the test procedures used during design validation and production testing.
By refining these procedures, you ensure that similar issues are detected and resolved early in future production cycles. This continuous feedback loop helps improve both product quality and reliability, ultimately leading to a more robust and field-ready product coming off the production line.
Before launching the product, several critical elements beyond the product itself must be prepared to ensure, [1] a smooth market entry and, [2] a smooth user experience. These include:
█ Product Certification
The product must comply with relevant certification standards based on its features and the regions where it will be sold. This could include safety, electromagnetic compatibility (EMC), wireless communication and environmental standards, among others. Each target market (e.g., CE for Europe, FCC for the US, BIS for India etc.) may have different requirements.
█ Product Documentation
Comprehensive and accessible documentation is essential. This should include:
● Detailed product page on the company website.
● Quick introduction or unboxing video.
● Technical datasheet outlining specifications.
● A clear and concise User Manual.
● Setup guides and troubleshooting tips.
● A dedicated support channel or helpdesk for customer assistance.
More Specifics...
Firmware engineering and Embedded high-end audio automation systems go beyond a simple one-page overview. These systems rely on real-time processing, precise control and acoustic tuning to optimize performance. Embedded microcontrollers and DSP chips handle dynamic range compression, noise reduction, multi-channel synchronization. Automation with remote diagnostics and system optimization. For a deeper understanding of the technologies behind our professional audio solutions, feel free to reach out by phone or email.
Operational excellence drives results
A review of project outcomes and supporting data shows that 92% of our projects met the agreed development timeline, a steady improvement from previous years. This progress is the result of ongoing enhancements to our workflows, proactive risk management and improved team coordination. We remain committed to refining our approach to ensure your product is delivered reliably and on schedule.